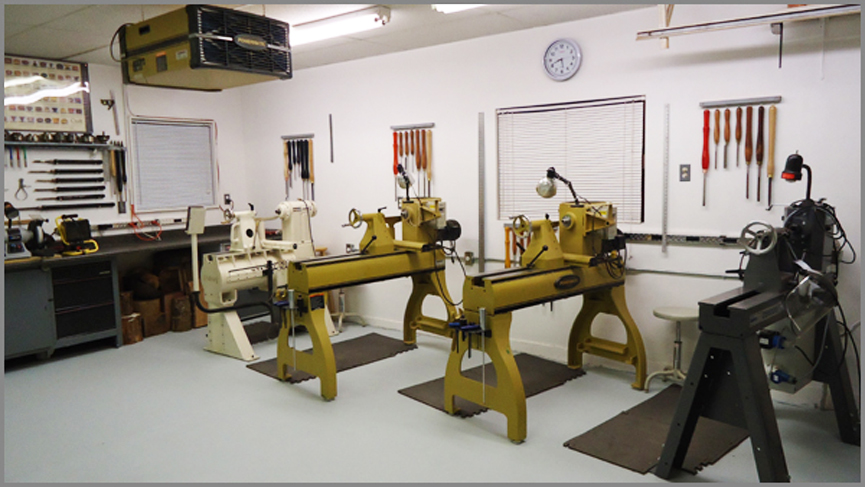
The patent-pending negative rake carbide cutters are a gamechanger in the woodworking field. These cutters allow for safer and smoother cutting, which makes it possible to transform super-hard woods as well as man-made materials without having to sand. The smooth cuts will also reduce the time required to re-polish the project. Negative rake chopper are safer and easier to use than traditional carbide cutters.
Cutting forces are decreased with positive rake carbonide cutters
Positive rake angles in carbide cutters are more effective at reducing cutting forces. They can reduce chip load and sustain higher cutting forces. These types of cutters also have greater chip-reduction capability, as a positive rake cutting edge has a thicker wedge than its counterpart. However, the chip-reduction ability of positive rake carbide cutters is only a qualitative indicator, and it depends on other factors, such as the thickness and the strength of the wedge. The thinner wedge associated with positive rake is more prone to breakage under high chip load and machine vibration. The thinner wedge also breaks down during impact loading, resulting in a poor machining productivity.
The relative orientation between the cutting face and the work is known as the rake angle. There are two types if rake angles. Positive rake refers a rake that is less than 90°. The negative rake carbide cutter is characterized by a blunter cutting edge and a less sharp rake. Both negative and positive rake carbide cutters both have pros and cons.
Cutters made from negative rake carbide produce better cuts
Use negative rake carbonide cutters to ensure a smooth, safe cut. These tools will make it easy to cut super-hard woods or man-made materials. These tools will make your work easier and less time-consuming. These cutters are also made to last for a long time. An average Negative Rake Carbide Cutter will last for approximately 80 hours.
Easy Wood Tools invented the negative rake carbide cutter. This type cutter can make better cuts in acrylics and hardwoods. It also has a longer lifespan. These cutters include a replacement 4-40 countersunk screw. This carbide cutter is also equipped with the three best G's of Carbide. They are a great investment for your woodworking project.
TiN carbide cutters reduce cutting forces
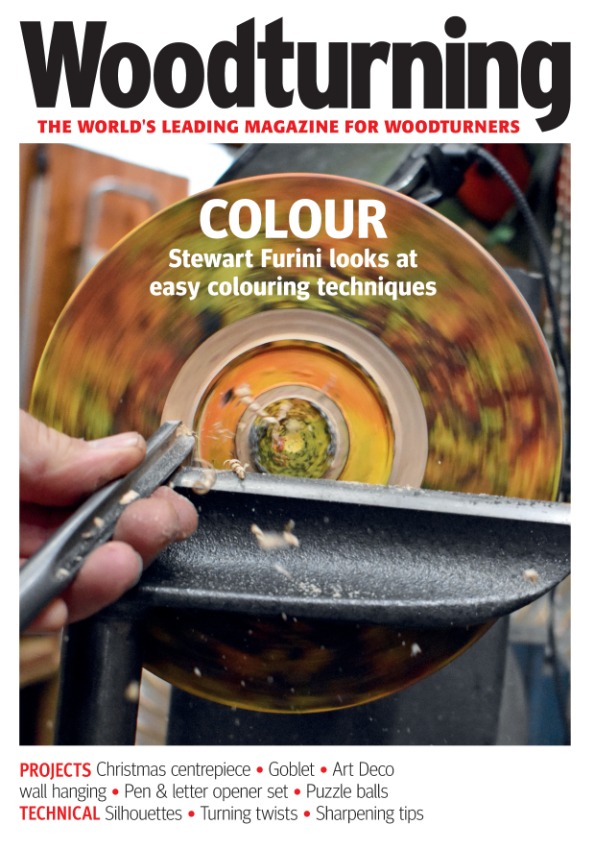
TiN carbide cutting tools produce lower cutting forces than standard tools. However, TiN carbide cutting speeds do not directly affect the cutting force. A signal-to noise ratio (SNR), model was employed to determine how process parameters affect the cutting force. This model helps to estimate the impact of cutting parameters on the forces.
Two types of carbide tools were used to study the cutting force: one was made from uncoated carbide, the other with Titanium Nitride's (TiN), coating. They measured flank and crater wear using optical microscopy and machine vision systems, and cutting forces were monitored using a dynamometer. The TiAlN, carbide-coated tool gave the best response when cutting forces were applied.
The experiment results show that the temperature in TiN-coated Titungsten carbide cutters can change with changing cutting parameters. Line I heats up slowly at 280360/min, while Line J heats up quickly at 320440/min. The TiAlN-coated tools saw a significant increase in temperature due to the increased feed per tooth.
Authentic Easy Wood Tool negative rake carbide cutters
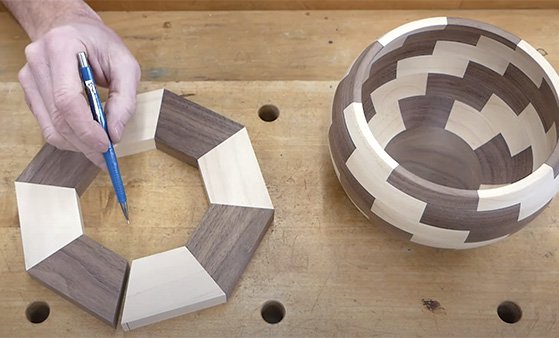
When you are looking for a quality cutting tool, one of the best choices is the Authentic Easy Wood Tools negative rake carbide cutters. These tools are manufactured in the USA and are designed for use with the Easy Wood Tools Mini and Pro Size Roughers and Micro Detailers. These carbide cutters with negative rake provide a smoother surface with fewer "grabs". They are made from the highest grade carbide to ensure maximum performance.
Easy Wood Tools' carbide cutters reduce chipping, catches and other problems when working with man-made material. They reduce chipping, eliminate the need for sharpening, and provide an ultra-smooth finish. The carbide cutting edges are supported directly under the workpiece. This allows the wood to absorb the pressure. Easy Wood Tools' negative rake carbide cutters work well for woodturning projects.
FAQ
What kinds of woods are good for making furniture?
Woods are classified according to their hardness. Softwoods can be pine, fir or cedar. They are great for outdoor furniture as they resist rot. Hardwoods include oak, maple, mahogany, and teak. Because they can't weather outside, they're usually used indoors.
How long does a piece take to finish?
It depends on the type and complexity of your design as well as the amount of finishing that you use. Hardwoods require more care than softwoods. Hardwoods are also more expensive than softwoods. They last longer and are more resistant to moisture. The average time it takes to finish furniture is one week to three weeks.
Can I make my living doing this job?
Yes! In fact, most woodworkers already have it. According to the U.S. Bureau of Labor Statistics (BLS), the median annual wage for woodworkers was $34,000 in May 2012. This is more than the national average of 31,000 per annum.
Which wooden items are very popular?
These wooden products are the most popular. They were made from sustainably harvested wood.
Oak, cherry and mahogany are the most sought-after wood types for furniture.
These woods are strong and durable, with beautiful grain patterns. They can also last for years if they are properly cared for.
Wooden furniture should always be painted first to protect against moisture damage. This covers all surfaces, drawers included, as well as doors and handles.
Paint that is water-resistant will ensure furniture lasts for a long time.
A high-quality oil-based primer should be used, followed by two coats with top coat. Depending on the amount of wear, you may need several coats.
You should avoid using aerosol paints or spray cans. These products contain solvents which evaporate quickly and leave behind harmful fumes.
Can you teach yourself woodworking?
You can learn everything best by doing. Woodworking is an art that takes patience, practice, skill and experience. To master any craft, it takes time.
To actually learn something is the best way. Start small and learn from your mistakes.
Where can I buy woodworking supplies?
There are many places that you can find all the information you need. You could also visit hardware stores in your area or shop online at Amazon.com.
You can also check garage sales and flea markets for old furniture and other materials you can reuse.
What is the difference between plywood and particle board?
Plywood is made of layers of wood that are pressed together under pressure. Plywood comes with a range of thicknesses, and it is most commonly used for flooring and cabinets. Particle board consists of sawdust mixed and resin. The resin is then compressed into large blocks. This board is commonly used in home improvement projects. Both boards are strong and can be easily cut.
Statistics
- Overall employment of woodworkers is projected to grow 8 percent from 2020 to 2030, about as fast as the average for all occupations. (bls.gov)
- Most woodworkers agree that lumber moisture needs to be under 10% for building furniture. (woodandshop.com)
- The U.S. Bureau of Labor Statistics (BLS) estimates that the number of jobs for woodworkers will decline by 4% between 2019 and 2029. (indeed.com)
- Woodworkers on the lower end of that spectrum, the bottom 10% to be exact, make roughly $24,000 a year, while the top 10% makes $108,000. (zippia.com)
External Links
How To
How to join wood with no nails
Woodworking is an enjoyable hobby. Woodworking can be a fun hobby because you can work with your hands to make useful objects from wood. There are times when two pieces of wood need to be joined together. This article will teach you how to do this to keep your woodwork projects looking great.
The first thing you'll need to do is cut off any rough edges from your pieces of wood before joining them together. Do not leave any sharp corners as they could cause problems down in the future. Now it's time to start glueing your boards together.
If you are working on hardwood, you should only use glue on one side. For softwoods like cedar and pine, glue should be applied to both sides. Once you have applied the glue, press down on the boards until they are fully attached. Before you proceed to the next step, be sure to let the glue dry completely.
After you've glued your boards, you'll want to drill holes into the joints where you plan to insert screws. Depending on what type screw you choose, the size of these holes will depend on how big they are. If you plan to use a 1/2 inch wood screw, drill a hole at least 3/4 inches in depth.
After drilling your holes, drive the screws into the board's backside. Avoid hitting the board's top surface. Otherwise, you could ruin the finish. Try to not hit the ends of the screws when driving the screws. This will prevent splitting the wood's end grain.
Once your project is complete, it's time to protect it against the elements. You can either seal the entire piece of furniture or cover the top. You want it to last years, so you can use any product. There are many options: oil-based varnishes; polyurethane; shellac; lacquer.
These products can generally be found in any home improvement shop. You should make sure you are getting the right type for the job. Don't forget to keep in mind that some finishes are toxic. Always wear protective gear when handling any of these finishes.