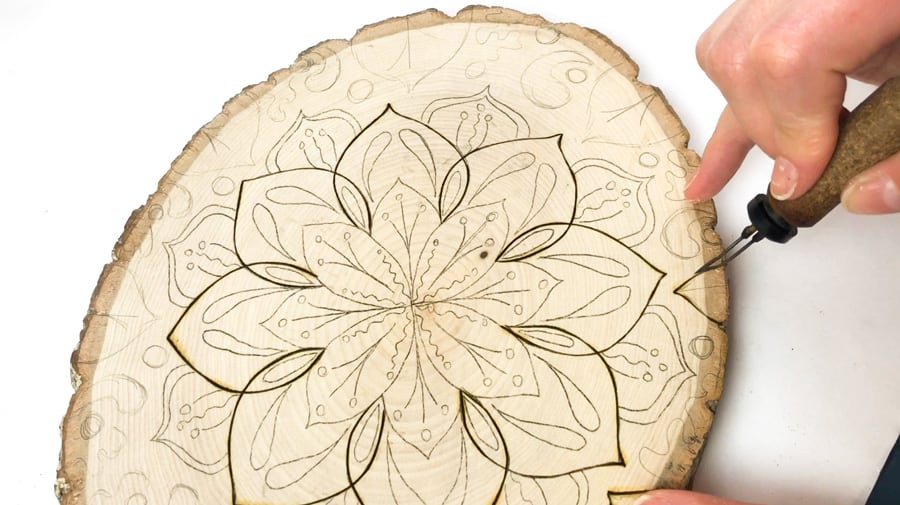
A wood burn project might be a good idea if you want to gift your children something truly unique. It's a great way to let your children express their creativity. A wooden toy made with their drawings can be a special keepsake. To give a special gift, you can use a template to burn the drawing that your children made.
Avoid burning wood that has a dark, grainy or resinous color.
Before you burn wood, make sure you know which type you are going to be using. For certain purposes, some wood types are better than others. Choose a wood that is relatively light and easy to split. Wood that is dark green or has a grainy appearance will need more seasoning. Lightly seasoned wood has darkened ends, visible cracks, and is relatively light. When struck with two pieces, it makes a distinct "clink". If you do decide to use wood that is dark and resinous, you should avoid burning pine.
The thickness of the final project should not exceed a third of the wood's width. Crafts should be no less than 0.38 inches (9.5 mm) thick. Thicker wood will crack and smoke easily. Plywood and paint will quickly fade your design. Resinous or painted wood will release toxic fumes into the atmosphere and produce toxic fumes.
For pyrography, lighter woods are better. Lighter woods are typically less expensive and have a smaller grain. Light woods do not have the same amount of resin, so they have the same density as dark-colored woods. For beginners, beech and other cheaper woods are good options. For those with limited budgets, you should be wary of woods with a grain pattern or glue.
Avoid using glue to burn wood
You can avoid burning wood by making sure that glue lines do not get too moist. Glue lines are normally more conductive than wood. The current is concentrated within the line area, which results in a quick cure. However, there are other factors that can contribute to burning, including the shape of the wood and other peculiarities of its anatomy. The following tips can help you to avoid burning wood that is too close to glue lines:
It is best to avoid using epoxy over wood.
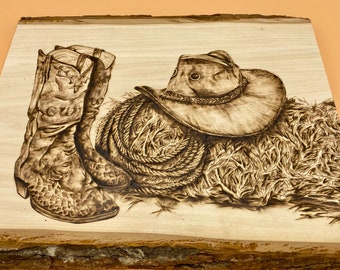
You might want to reconsider your safety precautions if you have been sanding a deck that has just been installed. Epoxy can cause breathing problems. Exposure to this chemical can result in sensitization, which can occur after a single or many exposures. You may experience skin irritation or respiratory problems. Inflammation of the respiratory system and skin are the most common effects of exposure to epoxy. Itching, rash, red eyes, and other side effects are also common. These reactions can range from mild to severe, but are unlikely to be life-threatening.
Wood is a great resource for making epoxy. While it can be expensive and not appropriate for every project, it is inexpensive and can be collected from fallen trees. Epoxy's main ingredient is volatile, so avoid burning wood. If you burn the wood directly over epoxy, it can cause a fire which can spread to the entire product. If you do decide to use this product, make sure you follow the manufacturer's directions to avoid damaging the finish.
Mixing epoxy requires gloves. You should wear gloves when mixing epoxy. It will harden quickly. It is just as simple as pouring water into it. The only difference is the epoxy can run into other parts of the wood so make sure to pour it evenly. Applying epoxy with a foam brush won't create the perfect surface.
FAQ
Do I have the potential to make a decent living doing this?
Yes! Many woodworkers are already doing so. According to the U.S. Bureau of Labor Statistics (BLS), the median annual wage for woodworkers was $34,000 in May 2012. That's higher than the national average of $31,000 per year.
How can a woodworker start making money?
Many people are starting to learn how to build furniture because they want to start an online business. If you are just starting to build furniture, there are many other ways to make money than selling on Etsy. Local craft fairs and events are great places to sell your products. Offering workshops could be another option for those who are interested in learning how to build their furniture. If you have experience as a carpenter or builder, you might consider offering services such as remodeling homes or creating custom pieces for clients.
What material would you recommend to start learning woodworking?
Start off with softwood like pine and poplar. You will feel more comfortable with these softwoods, so you can move onto hardwood.
Where do I start with woodworking?
Learning how to build furniture is the best method. You'll need tools, and you'll have to make mistakes along the way, but if you keep at it, you'll eventually figure out what you're doing.
Begin by choosing the project that you want to finish. It can be something as simple and small as a box, or large-scale as an entertainment center. After you have decided on a project to work on, contact a local woodworker that specializes in this type of work. Ask your local woodworker to help you determine the right tools for you and where they are located. Ask if you can find someone who does this kind work.
How can I learn basic woodworking skills
A great way to start learning how to build furniture is by building a simple bench for yourself. You can do this project using any type of wood you have on hand at home. You don't need to know which type of wood you should use. Instead, get some pine boards at Lowes or Home Depot. You'll need to sand the bench after it's built. Then, finish it with varnish or a stain.
How do I organize my shop?
The first step toward keeping your workshop clean and organized is to set aside a designated area for storing tools. Your tools will stay sharp and ready to go when they are free from dust and debris. You can hang tools and accessories with pegboard hooks.
Statistics
- Woodworkers on the lower end of that spectrum, the bottom 10% to be exact, make roughly $24,000 a year, while the top 10% makes $108,000. (zippia.com)
- The U.S. Bureau of Labor Statistics (BLS) estimates that the number of jobs for woodworkers will decline by 4% between 2019 and 2029. (indeed.com)
- Most woodworkers agree that lumber moisture needs to be under 10% for building furniture. (woodandshop.com)
- If your lumber isn't as dry as you would like when you purchase it (over 22% in Glen Huey's opinion…probably over 10-15% in my opinion), then it's a good idea to let it acclimate to your workshop for a couple of weeks. (woodandshop.com)
External Links
How To
Tips on how to drive a nail in wood
It is essential to pick the right size and style of hammer before you can drive a nail in wood. The most commonly used types of Hammers are claw hammers. Each kind of hammer has its own advantages and disadvantages. A claw hammer, for example, is the best choice if you need to hit nails hard. However, it's not easy to know exactly where the impact will land. The sledgehammer works well for large areas, but is too heavy for smaller tasks.
After selecting the right hammer, you will need to place your hand flat against one side of the head. The handle should rest comfortably in your hands. Hold the handle in your hand, but don’t force it too hard that you break. Hold the hammer straight up, keeping your wrist relaxed. You should then swing the hammer straight up, keeping your wrist relaxed. You should feel the impact of your hammer hitting the nail. You can practice swinging the hammer with a block or wood until you feel the rhythm.
The hammer should be held close to your body when you are ready to begin driving the nail. To ensure that the nail is perpendicular on the surface of the wooden floor, position it. Keep your focus on the tip of each nail. Swing the hammer forward, then follow through with the motion of the hammerhead. You can repeat this several times, increasing your swing speed. Once you've mastered the technique, try adding power to your swings. Then, raise the hammer from your shoulder to bring it down. This way, you'll be able to put more energy behind your blows.
Once you have successfully drilled the first hole in the nail, remove the hammer. To remove the remainder of the nails, you can use a screwdriver/pry bar. Keep the nail heads parallel to the board's surfaces in order to avoid splitting wood.